Dettaglio
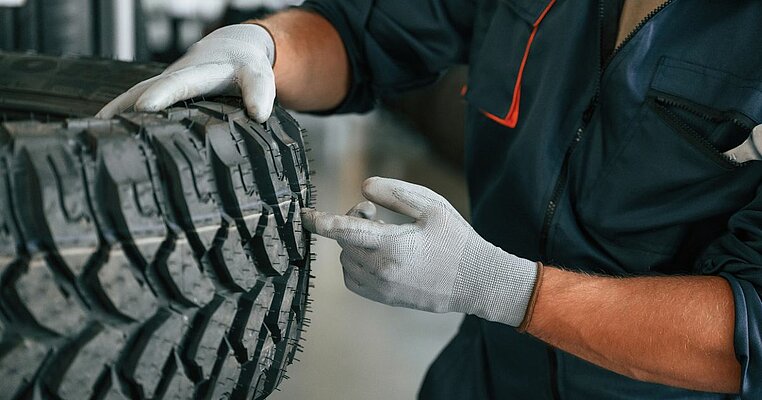
Di Maria Carla Rota
La sfida: pneumatici 100% circolari
In Europa nel 2023 sono stati generati circa 4,2 milioni di tonnellate di pneumatici usati, secondo una stima di Astutus Research, riportata dall’Associazione europea dei produttori di pneumatici e gomma (ETRMA): di questi, una quantità pari a circa 600.000 tonnellate è stata destinata al riuso o alla ricostruzione, mentre la parte restante, circa 3,6 milioni di tonnellate, era costituita da pneumatici fuori uso. A livello globale, invece, ogni anno vengono prodotti circa 1,6 miliardi di PFU per un totale di 26 milioni di tonnellate (fonte: Cordis).
La prospettiva per i prossimi decenni è quella di un ulteriore aumento, legato alla crescita del numero dei veicoli, che arriveranno intorno ai 3,4 miliardi a metà degli anni 2040, principalmente su spinta del settore automotive dell’area Asia-Pacifico. Di conseguenza, secondo l’Energy Transition Outlook 2023 della norvegese DNV, entro il 2030 ci saranno fino a 5 miliardi di pneumatici usati: l’incremento sarà più rapido rispetto a quello dei veicoli, soprattutto per via della diffusione delle auto elettriche, la cui quota di mercato dovrebbe passare dall’8% attuale al 96% entro il 2050. Questa transizione ridurrà la durata degli pneumatici a causa dell’aumento del peso e delle capacità di accelerazione delle auto green, accrescendo quindi la necessità di sostituire i copertoni. Considerata la prospettiva, è urgente spingere il comparto ad abbracciare il prima possibile i principi dell’economia circolare anche in Italia.
PFU in Italia: i dati
Nel nostro Paese, secondo gli ultimi dati diffusi dall’ISPRA (Istituto Superiore per la Protezione e la Ricerca Ambientale) nel 2022 sono state gestite circa 520.000 tonnellate di pneumatici fuori uso, a cui si aggiungono circa 84.000 tonnellate esportate all’estero. La gran parte dei PFU raccolti è avviata a recupero di materia (85,4%), ma la raccolta deve essere implementata ulteriormente per garantire che tutti i flussi di rifiuti di pneumatici siano debitamente valorizzati.
Come previsto dalla normativa, anche ai PFU si applica il principio della gerarchia dei rifiuti, secondo cui la gestione debba ricondursi alla seguente scala di priorità: ricostruzione degli pneumatici divenuti rifiuto (preparazione per il riutilizzo); recupero di materia (riciclo); recupero di energia (recupero di altro tipo).
Come avviene il processo
Le aziende autorizzate alla raccolta, iscritte all’Albo Gestori ambientali in cat. 4, effettuano il prelievo presso i generatori, ovvero le persone fisiche o giuridiche che nell’esercizio della loro attività imprenditoriale generano PFU. In funzione di criteri di ottimizzazione, si può decidere di eseguire una fase di stoccaggio intermedio o di conferirli direttamente presso gli impianti. Qui si procede con la prima fase del trattamento, la stagionatura, utilizzata principalmente per pneumatici di medie e grandi dimensioni, che ha lo scopo di rimuovere l’acciaio armonico presente sulla “spalla” dello pneumatico.
Si passa poi alla frantumazione: grandi cesoie rotanti eseguono meccanicamente una prima riduzione volumetrica, producendo “ciabattato” di dimensioni da 5 a 40 cm, adatto per la valorizzazione energetica in impianti ad hoc, principalmente cementifici, grazie al potere calorifico pari a quello del carbone, ma con emissioni climalteranti nettamente inferiori.
In alternativa, si procede con una seconda frantumazione del ciabattato, mediante azione fisica e/o meccanica, fino a raggiungere le dimensioni di 10-25 mm, generando il cosiddetto “cippato di gomma”. Inoltre, in questa fase avvengono la separazione e il recupero di buona parte dell’acciaio armonico.
Con la terza frantumazione, infine, oltre a recuperare la frazione residuale dell’acciaio, il materiale viene reintrodotto all’interno dei mulini per ridurre nuovamente volume e granulometria. Nascono così il granulo e il polverino di gomma, che trovano diverse applicazioni, dai campi sportivi all’asfalto, dai pannelli fonoassorbenti ai sigillanti.
Obiettivo: circolarità
L’obiettivo sul lungo periodo è quello di arrivare a produrre pneumatici 100% sostenibili, sostituendo, almeno in parte, i materiali vergini con quelli riciclati. Trattandosi di prodotti altamente tecnici, però, è necessario trovare un equilibrio tra sicurezza, durata ed efficienza energetica. La riduzione dell’impatto ambientale, insomma, non deve andare a scapito degli alti standard di prestazione: un compito non semplice, quando si sostituiscono i materiali fossili.
A questa sfida lavorano da tempo i reparti R&D di molte grandi industrie globali del settore, che stanno dedicando energie e creatività alla ricerca di soluzioni di alto valore, tanto dei processi di produzione quanto del prodotto finale. A questo proposito in Europa va considerata anche la normativa Euro 7, che introduce specifici limiti di emissioni inquinanti anche per gli pneumatici, che dovranno diventare più durevoli e resistenti all’abrasione da rotolamento.
Tra le sperimentazioni in corso, l’americana Goodyear Tire & Rubber Company nel 2022 ha presentato un prototipo di copertone realizzato al 70% con materiali sostenibili di origine biologica oppure provenienti dal riciclo, in pratica scarti di riso e rifiuti di plastica, dandosi il traguardo di realizzare entro il 2030 gomme al 100% circolari. Tra i materiali del futuro, anche la corteccia di guayule, la radice di tarassaco russo e il butadiene, componente della gomma, ricavato da biomasse di origine vegetale.
In questo contesto di ricerca si inserisce anche BlackCycle, progetto europeo finanziato da Horizon 2020, conclusosi nel 2024, che ha elaborato un modello di economia circolare per dare nuova vita ai PFU. “Grazie allo sviluppo di cinque nuovi processi e di quattro nuove materie prime seconde, abbiamo potuto ridurre in modo significativo le emissioni di gas serra rispetto ai tradizionali metodi di recupero dell’energia e di riciclaggio chimico”, spiega il coordinatore Jean-Michel Douarre. “Il nuovo nerofumo sostenibile e recuperato emette meno CO2 di quello vergine per tutto il suo ciclo di vita. Inoltre, il recupero di polvere di gomma micronizzata dallo strato interno comporta emissioni di CO2 tre volte inferiori rispetto alla produzione di nuova gomma per il rivestimento interno”.
Carbon black e olio di pirolisi
Al centro di questo progetto, come di altri studi e sperimentazioni, c’è la pirolisi, processo ad alto calore in assenza di ossigeno, che scompone i pallet di gomma in tre parti: gas, che serve ad alimentare il processo stesso, materiali solidi, da cui si recuperano nerofumo (rCB, carbon black recuperato) e minerali, e infine olio, noto come olio di pirolisi da pneumatici (TPO), o catrame di pneumatici grezzo.
Il carbon black è un agente di rinforzo essenziale per la gomma, di cui migliora resistenza, elasticità e durata. Negli pneumatici, oltre a garantire robustezza, conferisce anche il colore nero. Quello recuperato dalla pirolisi, però, attualmente non può sostituire integralmente il carbon black vergine (vCB), ma solo in parte, perché contiene anche residui inorganici o carboniosi fino al 40%. La standardizzazione della qualità è una sfida cruciale per i produttori, che devono garantire tracciabilità e rigido controllo dei processi.
A loro volta i TPO, noti anche come oli di termolisi, si distinguono per alta aromaticità e basso contenuto di zolfo. Sono adatti a molteplici applicazioni industriali: anche in questo caso, a seconda della qualità, possono essere usati nel settore petrolchimico o raffinati per produrre carburanti sintetici e diesel rinnovabile.
Sia rCB che TPO offrono un’alternativa più sostenibile agli equivalenti di prodotti vergini in termini di impronta di carbonio ed efficienza delle risorse: per questo motivo acquisiranno sempre più importanza in UE, dove nel prossimo decennio il Green Deal 2.0 e il Circular Economy Act potrebbero introdurre obiettivi ancora più severi nell’ambito delle principali direttive sui rifiuti e sul riciclaggio.
I quattro dati dal mondo
1,6 miliardi: numero di PFU generati ogni anno a livello globale (fonte: Cordis)
3,6 milioni di tonnellate: peso dei PFU generati in Europa nel 2023 (fonte: Astutus Research, ETRMA)
520.000 tonnellate: quantità di PFU gestiti in Italia nel 2022 (fonte: ISPRA)
84.000 tonnellate: quantità aggiuntiva di PFU esportati dall’Italia all’estero (fonte: ISPRA)